ISOの下準備スキルマップ・洗い出しと採点
前回のルール作りで概要が見えた方はご理解いただけるのでしょうが、ルールを作るためにガイドライン的な部分が欠けています。それが今回のお話のスキルです。スキルが高ければ、より高度な作業が可能になったり、高い知識を吸収することが可能です。
今回の話は、ISOに限定しません。基本はISOでの活用を目的としていますが、より多くの方に取り入れていただければと思います。
また、ISOのピラミッドの頂点とスキル(スキルマップ)を繋ぐことがISOの運営を楽にする事もご理解いただければと思います。
今回の目線はこちら
- スキルの洗い出し、目安とその数。
- 評価の方法は単純に
- 総評価数値の下がるスキルマップの設計
- 多能工は前の工程から
スキルの洗い出し、目安とその数。
スキルの洗い出しは工程の洗い出しになります。今回は、今までより具体的な例を挙げてお話を進めていこうかと思います。世の中ではスキルは多い方が価値があります。「あれもできる・これもできる」となると、その人の価値は高くなる傾向にあります。ですが管理の基準で考えると多すぎる管理項目は混乱を招きます。かと言ってうまく管理できないと微妙な能力になってしまいます。
スキルを管理するためのスキルマップの項目は、1人25~30項目に抑えましょう。それ以上は、薄く混乱を招きます。
工場でのスキル洗い出し
スキルの洗い出しをする際、作業面だけでない部分も見ていきましょう。
ここでは大カテゴリー5×小カテゴリー5程度を考えていきます。
例えば】
A君は加工機Aと加工機Bの担当です。
加工機には、立ち上げ(電源投入)・終了・メンテナンス・加工
この4項目は、必ず絡んできます。こう考えると小カテゴリー4項目が既に埋まっています。
大カテゴリー ⇒ 加工機A・加工機B
小カテゴリー ⇒ 立ち上げ・終了・メンテナンス・加工
この場合、A君は既に8項目のスキル管理を行う必要があります
この他に、図面の見方・工程内ルール・会社ルール…などを大カテゴリーに追加していけば直ぐに25~30項目などは埋まってしまいます。
あまり欲張らないようにスキルマップは考えましょう。もう少し先でお話ししますが、スキルマップは設計によって上がり続ける必要がないのです。最初から無理をしないように注意が必要です。
評価の方法は単純に
スキルの判断は可能な限り単純にしていきましょう。日本語は曖昧な表現が多いのでそこも注意しましょう。私は5段階評価をお勧めしています。
1 - 勉強対象
2 - 補助的作業ができる
3 - 指示があれば作業が可能
4 - 1人で作業ができる
5 - 新しい作業者へ教育ができる
総評価数値の下がるスキルマップの設計。
「明確な理由・誰もが納得する理由」があればスキルマップの総評価数値が下がっても問題はありません。その為には、設計が必要です。
品質マニュアルなどに、「スキルマップの見直しを年1回行う事」の記載が必要ですが。
例えば】
A君は1年後、加工機Cも作業するようになったとします。当然、加工機A・加工機Bのスキルが下がる訳ではないです。ですが、スキルマップの大カテゴリーが一つ増えます。
A君は5カテゴリーから ⇒ 6カテゴリーに管理項目が増えることになるのです。
こういった現象を先読みしてスキルマップの総評価数値は「%」にしておくと便利です。
1年目20項目の「小カテゴリー」を管理してスキルマップを作ったとします
20項目を5段階評価するので
最低得点は 20点
最高得点は 100点となります。
1年目終了時 80点だったとします。
翌年(2年目) 1つの大カテゴリーが増え、小カテゴリーが5項目増えたとすると
最高得点は 125点となります
昨年の 80点+項目が増えた分の5点を足して
2年目のスタートは85点からとなります。
1年目の総評価数値は、
80点(最終点数)÷100点(最高得点)
= 0.8 ⇒ 総評価数値は 80% となります。
2年目(スタート時)の総評価数値は
(80点(昨年の実績)+5点(今年の追加分))÷125(最高得点)
= 0.68 ⇒ 総評価数値は 68% となります。
このように 1年目終了時 80%の総評価数値は、2年目のスタート時、68%の総評価数値に下がります。
スキルマップを常に上げていく設計にすると、新卒と勤続10年の社員の一向に縮まらないスキルマップになります。また、青天井のような点数評価もおかしな評価ではと思います。全社員が前向きに毎年学んでいけるよう総評価数値の見直しは必要だと考えます。
多能工は前の工程から。
耳にされたことはないでしょうか?「後工程はお客様」このような言葉を。
その考えには勿論させいです。ですが私はもう1つ「依頼する側にもルールが必要」この言葉を大事に製造業を行ってきました。
- 全く数字の見えないFaxでの製造依頼
- 寸法の抜けている図面の製造依頼 などなど
誰もが一度は受けたことのある事例ではないでしょうか?このような事は日常で製造業の方は誰もが頷くのではと思います。
「少しでいいから図面のチェックで随分解消されることなのに…」と思います。
日常で起こっている、このような現状を打破し、より良い製造環境を整えるためには、後工程より前工程の方が大事になる場合があります。
何故なら工程を覚えることにより、要望が出しやすくなるからです。
後工程を考えるのは割と当たり前で、そのような教育をしている所は多いようですが工程を遡る事は、後回しになりがちです。是非、取り入れてみてください。
まとめ
ISOの取得・運用は、スキルマップとISOの目標・方針を繋げばISOの運営は比較的簡単です。
要は、ISOの設計(取得・運営)には、スキルマップが非常に重要な位置づけにあります。間違った運営方法を取るとISOのためだけに資料を作ったり行動を起こしたりが必要になりISOイコール負荷業務に繋がるでしょう。
- ISOとの繋がり
- スキルの洗い出し
- 年1回スキル見直し
これに「文書化した情報を保持」を繋げた(肉付した)ルールができれば最短・最強のISOになることでしょう。
単純・繊細なスキルマップをお考え下さい。
ISOは製造業に限らず対応は可能でしょう。次回また機会があれば具体的な運営に関するお話ができればと思います。
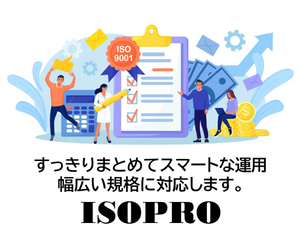
ISOの資格取得は、ものすごいボリュームです。
外部機関のコンサルへのご相談も近道の一歩です。