【板金設計】薄い板にネジを締めたいその方法と選択
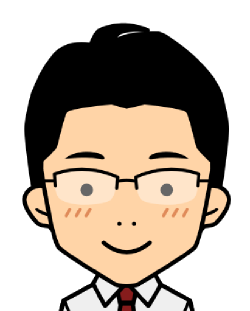
こんにちはクロです
薄い板にネジを締めたい
こんな悩みはありませんか?
どんな方法があるの?
今日は、そんなお話です。
ネジを締める方法を考える
設計を行っていく最中にメンテナンスを考えると、どうしてもネジでの着脱を考えた構造にぶち当たることがあります。以前ご紹介した「板厚とネジの関係」は素直に板金にタップ加工を行うお話でしたが、今回は他の方法も考えてみます。
板金に少しの加工でねじ止めができるようにするには…
- 板金にタップ加工を行う
- 板金にバーリングタップの加工を行う
- ナットを溶接する
- クリンチングを圧入する
一般的にはこの4つのほうほうでしょうか?
いつものことですがメリットとデメリットがあります。その部分が選定理由に繋がりますので紐解いていきましょう。
4つの加工方法・メリットとデメリット
加工方法の種類があるということは、その加工が必要な使われ方があるということです。
先ずは、どのような加工があるかを確認していきましょう。
直接のタップ加工
板金加工にネジを締めるための一般的な方法
メリット 加工コストが一番安いです。
デメリット は板厚に対しての加工可能なサイズが最も厳しいです
バーリングタップ加工
ネジ締めの際、板厚によるネジ山不足の解消に利用される可能性がある加工法
バーリング加工(金型による成形加工)後タップ加工を行う。
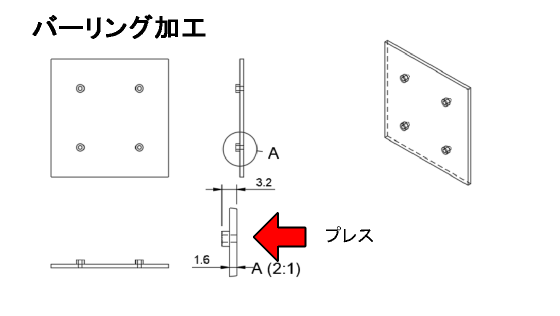
材質・板厚によるが、バーリングの高さは
基本板厚×1.0~1.2倍 が高さの限界とされる。
※1.6㎜なら × 1.0倍 =1.6㎜(バーリングの高さ)
1.6㎜(本来の板厚)+1.6㎜=3.2㎜(全体高さ)となる。
メリット 追加部品なしで通常のタップよりネジを切る肉の部分が多くなる
デメリット 工程が増えるためコストが上がる 金型が必要 安全基準の幅が狭い
ナット溶接
バーリングタップで対応できない、大きめのネジサイズのものが多く利用される。通常のナットに近い物を溶接するため締め付けの強度への安心感は一番
利用されるナットは通常のナットでも可能だが、溶接ナットと呼ばれる溶接を目的にしたナットが使われることが多い。
メリット 母材の強度もあるが、どのようなサイズのネジも対応可能
デメリット 部品のコスト溶接コスト
クリンチング
タップの切れない厚さや 薄く溶接の難しい素材にも対応している規格がある。
タップもバーリングも難しい、溶接で変形の可能性がある薄板などに利用されます。
加工方法も簡単で指定された下穴に押し込みプレス機で圧入工場内の作業としても比較的簡単な作業になります。
メリット 薄い板厚でも対応可能 溶接の難しい材質でも対応できる
デメリット ネジを締めるトルク管理がシビア
使い方を考える
タップ⇒バーリングタップ⇒溶接ナット⇒クリンチング
工数の少ないタップから、部品としての単価の高いクリンチングまで。
クリンチング⇒タップ⇒バーリングタップ⇒溶接ナット
どれだけ薄い板から加工が可能かを考えました。溶接ナットは薄すぎると変形の可能性があるためこの順番です。
タップ⇒バーリングタップ⇒クリンチング⇒溶接ナット
タップ・バーリング加工はタレパンなら切る(抜く)加工と同時に行える可能性があります。クリンチングは作業での個体差が出にくいですが、溶接はどうしても村が出てしまう可能性があります。
溶接ナット⇒バーリングタップ⇒タップ⇒クリンチング
機械締めをした場合のトルク対応です。ネジの太さでトルクは決まっていますが、それ以上のトルクをかけてしまった場合の破損の可能性を考えています。
まとめ
コストや保障を考えると、タップ加工を第1選択肢となるでしょう。2番目としてはバーリングタップとなりますが、共に板金の板厚に係ってきます。板厚の薄いせいで加工が難しい場合、トルク管理をしっかり行うことを条件に、クリンチング加工となり、板厚が1.6㎜以上ありガンガンネジを締めたい!等の時は溶接ナットで対応ということになるのではと考えます。
