【板金加工】レーザー加工への理解・図面指示についてちょっと得する話
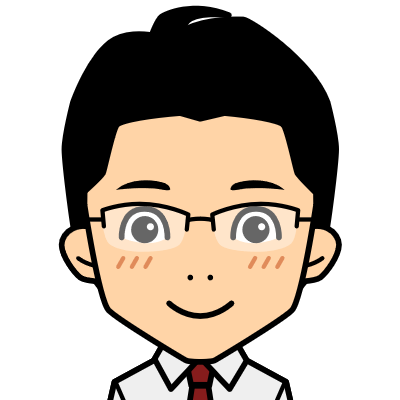
こんにちはクロです。
工場見学にい行くと「レーザー加工ってどうやって切るんですか?」こんな事をよく聞かれます。同じように形どるタレパン加工、こちらに関しては文具のパンチ(穴あけ機)の話をすると伝わりやすいのですがレーザーについては順を追って話をしないと勘違いされそうですし、図面指示で得する部分もあったり!
今日はそんなお話を♪
加工者ではなく依頼者としての知識
Co2レーザーとか窒素とかファイバーとか…難しいことは工場にお任せして、依頼者として知っておくと良いのでは?そんなお話です。設計に少しでも取り入れることができる。「最終的にはコストが!」この部分が狙いです。
専門用語の必要性
難しい話をするつもりはないのですが、それでも最低限お話を進めていくためにも必要な用語を少し説明させていただきます。ある程度の専門用語を使わないと文章がだらだら長くなりそうなので最初にご案内です。
ピアス(ピアッシング)
レーザーを照射して穴をあける行為。必要な軌跡(カットライン)にピアスを入れると、溶けて必要なラインが保てないため、必要な軌跡より少し離れたところピアスをあけ加工をスタートする。
アプローチ
ピアスから必要な軌跡までの道中をアプローチと呼びます。長すぎると過剰加工になり、短すぎると軌跡に影響が出る可能性があります。
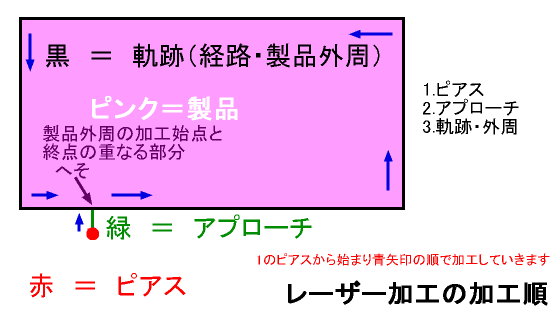
ドロス
レーザーで熱をかけることによりできる酸化物(溶融物)板厚が厚いほど発生率は上がる。加工機のメンテナンスにより、ある程度抑えることは可能。レーザーの最初の軌跡と最後の軌跡が交わる部分でも発生する。ドロスは堆積物です。レーザーが稼働すればするほど加工機のいたるところに堆積していき、ある程度の周期でメンテナンスが必要です。メンテナンスの手抜きは、ドロスを生み出す一つの原因になります。
バリ
加工中に酸化したものがドロス。酸化せず残ったものがバリと呼ばれる。溶けて粉状のものがドロスで小さな塊で残ったものがバリと呼ばれる。タレパン加工のバリや樹脂加工のバリとは少し出来方が違います。
スパッター
最初のレーザーの照射時に飛び散る粒子。見た目は工事現場の火の粉のように見えることもある。加工中でも加工金属上の不純物(微量の油の塊・埃など)上をレーザーが通過することにより発生することもある。現代の自動運転が主流になった加工機では回避行為は難しく、加工後に作業者の対応となる。
へそ
レザー加工は、ピアス⇒アプローチ⇒軌跡スタート⇒軌跡エンドと加工を勧めていきますが、大抵は軌跡のスタートとエンドは同じ場所になります。その部分を「へそ」と呼び処理が必要になる可能性があります。※処理とはヤスリで削る行為などです。
発生理由としては軌跡を一周してスタートとエンドが一致する場所で交差しようとすると
製品の自重で溶け落ちてしまうためです。
レーザーは本当に切っている?
変な見出しですよね…分かってはいるのですが詳しく調べれば調べるほどレーザー加工は「切っている」と言いにくくて。理由は動きを言葉にした時です。
レーザー照射⇒アシストガス噴出⇒レーザーヘッド移動
この動きで切っているように見えるのですが…実際はレーザーは金属を溶かしているだけでアシストガスの勢いでドロスを除去し切っているように見えているのです。ネットの検索などで板厚の厚い金属の破断面に縦の線が残るのはその為です。
溶かす⇒酸化物を吹き飛ばす⇒移動する
こう考えると切っているのかな???ってなります。
溶かす飛ばすの連続加工で発生するドロス・バリ
レーザー加工は、メンテナンスを毎日していても加工後の出来上がりでドロス・バリの発生を0にすることは難しいです。基本的には工場責任で除去するものですが、図面記載しておくとトラブル回避になりるかもしれません。
「バリ無きこととする」
※一言入れることの効果が、図面の強みですね。
バリ取りの方法
工場としてバリ取りの選択肢はいくつかあります。方法と効果などを考えてみます。
バリ取り機
紙ヤスリの付いた大きなローラーの機械を通すことにより、バリの除去を行う。製品全体にヤスリがかかるので、バリ取り後は錆びやすくなります。メッキ材には不向きで(メッキが剥がれてしまうため)SPHC・SPCCなど加工後、表面処理を行う製品に利用されます。
バレル研磨
あまり大きな製品は不可能。ドラム式洗濯機のような中に研磨剤と一緒に回転させバリを除去する。研磨剤の種類によって光沢を出したり、製品のエッジを削ったりと多様な加工が可能。これもメッキ材は向かない。
手加工
文字の通り、人が手で加工をする。人の手のため言いにくいが、作業にむらが出る可能性がある。だがどんな製品・素材も対応できる万能な方法である。
バリ取りと面取り同じじゃないですよ
お客様で「バリ取り」と「面取り」を明確に意識できていない人がいます。皆さんは違うと思うのですが、バリ取りは加工上発生してしまう可能性のあるもので、面取りは工程を追加しています。私の経験から出申し訳ないのですが、実際の組付け作業(利用現場)で立会させていただいたりすると「面取り必要ないな…」なんて事が多いです。
それとなく後で担当者さんと話をしたりすると面取り支持の理由が驚きで
- 図面に元から書いてあった
- 以前制作した図面で手直ししていない
- 周りの設計者がみんな記載しているので
今後は少し考えてみましょうか…ってなりますよね。
基本可動部でなければ面取り必要かな?って思っています。
面取りは立派な一つの工程です。
まとめ
ドロスの除去は工場の義務です。特に心配される必要はないと思います。問題はバリと呼ばれるもので、過剰な加工を追加しないような図面指示があると適正なコストに収まるのではと思われます。加工依頼時に相談できるのであれば、それに越したことはないのですが、ネットの利用などの場合は、「バリ無き事」などの記載で納品後のトラブルを回避できるのではないでしょうか?
